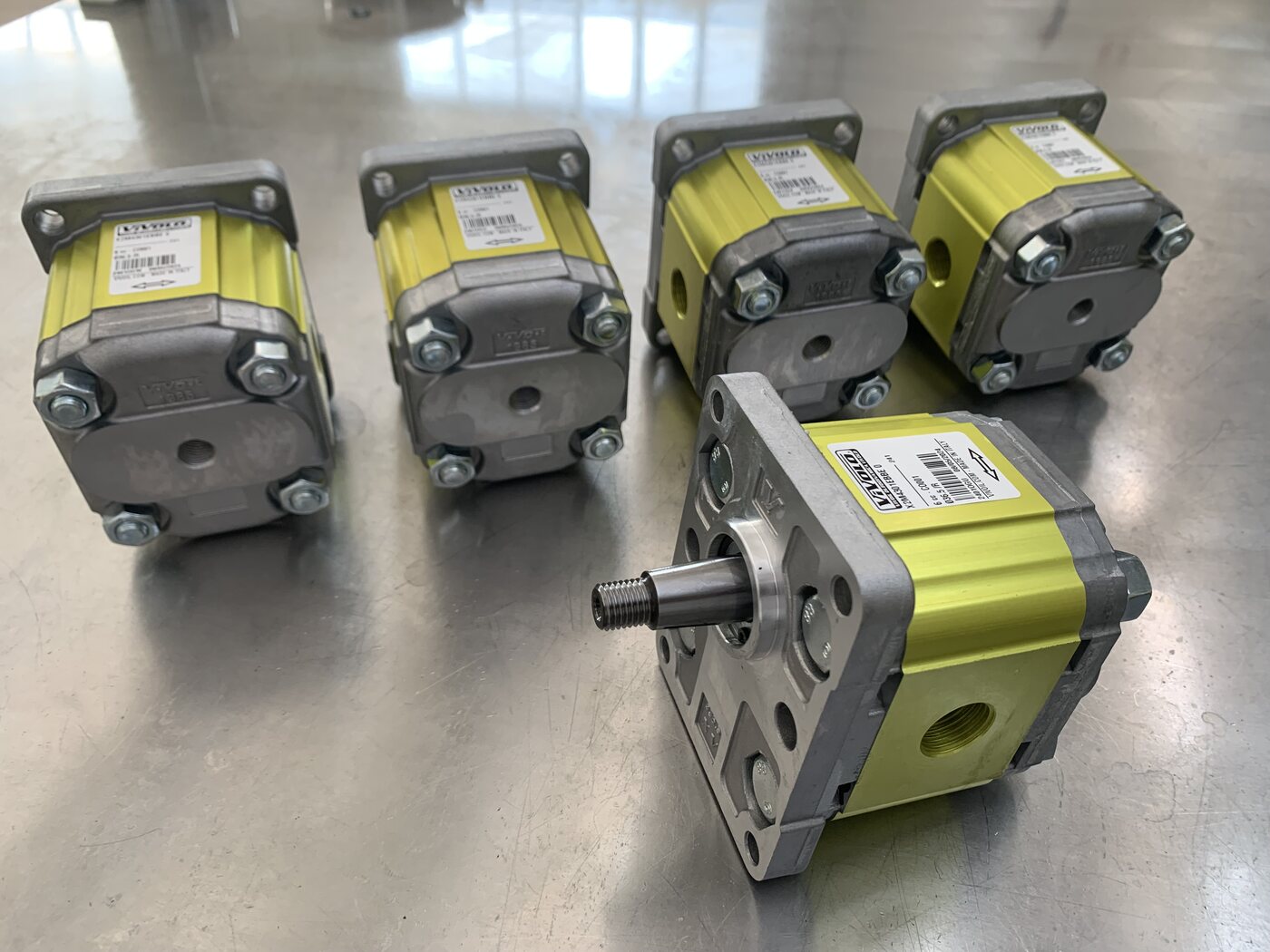
Looking for a Vivoil hydraulic motor for your project? Here’s a guide to help you identify the optimal component for your situation, with tips for choosing the right motor type and options. Also find our suggestions for installing it, keeping it running well, and special applications.
Table of Contents
What is a hydraulic motor and what is it used for
The hydraulic motor is a component that converts hydraulic energy into mechanical energy (as opposed to the hydraulic pump, which, on the other hand, converts mechanical energy into hydraulic energy). To learn more, read our article on the difference between hydraulic pumps and hydraulic motors.
How to choose the hydraulic motor for your project
The first step in choosing the right component is to identify the best type of motor for your project, based on the mode of operation. In fact, components of this type fall into two main types: unidirectional motors and reversible motors (also called bidirectional or bi-directional). Here are their characteristics and when to use them.
Unidirectional hydraulic motors
Features
Once inserted into the application, unidirectional motors can only rotate in one direction: right (clockwise) or left (counterclockwise). Depending on your needs, before installation, you can change the direction of rotation and turn a motor that was born to turn only clockwise into one that turns only counterclockwise and vice versa.
The operation is simple and almost always possible without changing any components. Excluded from this are types that have asymmetrical ports on the shaft flange, for which it will be necessary to replace these components if necessary.
Recommended when
You are looking for a motor that provides motion always in the same clockwise or counterclockwise direction, to be reversed possibly before installation.
Reversible hydraulic motors
Features
They are the most standard type. Once installed in the application, reversible motors can rotate in two directions-both clockwise and counterclockwise-without having to make any modifications. In the drawing below, you can see this schematically:
Recommended when
You are looking for a motor that can repeatedly change the direction of rotation during use, depending on the function to be performed.
One example: the rotation of a fan that periodically involves reversing the motion to clean the blades of dust.
Beware of imitation!
Imitation motors of ours, produced by companies with which we have no relationship, are for sale on the market. To recognize our original products from counterfeit ones, check:
- the label (all Vivoil products since 2010 have a label that is very difficult to remove)
- the trademark (all our components are engraved with the VIVOLO trademark)
If in doubt, we are available to assess through photos whether these are our own products or unauthorized copies.
Four dimensional groups
Having chosen the type of motor (unidirectional or reversible), move on to the dimensional group. To determine the most suitable group for your project, you must take into account:
- Input and output flow rate
- Rotational speed to be obtained on the shaft
- Working pressures
- Any specific requests for the type of attachment
From these parameters, you can select the most suitable size group. The motors in the Vivoil range are divided into 4 groups:
- Group 0 (displacement 0.45 cm3/rev — 2.28 cm3/rev, rotational speed up to 9000 rpm, maximum pressures achieved up to 280 bar)
- Group 1 (displacement 0.91 cm3/rev — 9.88 cm3/rev, rotational speed up to 6000 rpm, maximum pressures achieved up to 300 bar)
- Group 2 (displacement 4.2 cm3/rev — 39.6 cm3/rev, rotational speeds up to 3500 rpm, maximum pressures up to 300 bar)
- Group 3 (displacement 14.89 cm3/rev — 86.87 cm3/rev, rotational speeds up to 3000 rpm, maximum pressures up to 320 bar)
Customize your hydraulic motor
Once you have defined the direction of rotation and identified the size group, you can customize your motor according to the connections to be provided, choosing from:
- several front flanges
- several shafts,
- Different input ports and output ports both in position (in the two heads or in the motor body) and in type
Find the main variants on the page devoted to unidirectional motors and on the page devoted to reversible motors.
Here are some of the most commonly used customizations:
Flange and shaft
It is important to remember that shafts can only be applied to certain types of flanges. Therefore, by choosing a certain type of flange, you will have the option of selecting only certain types of shafts. In our catalogs you will find the possible combinations.
Drainage
In reversible motors, the standard drainage is external and serves to protect the oil seal from counterpressure that would cause it to eject. In unidirectional motors, on the other hand, standard drainage is internal.
This implies that the outlet pressure must be less than the resistance of the oil seal. Clearly, it is necessary that the pressure present in the drain not exceed the sealing pressure of the oil seal.
In unidirectional motors you can also opt for external drainage, but this is a special customization, not the standard and requires a dedicated code. In case, please contact us.
Reinforced oil seal
The reinforced oil seal consists of a supporting metal washer.
It represents the standard in Vivoil motors and is applied as often as there is sufficient space, raising the back pressure it can withstand, from 0.6 bar of the standard oil seal to 6 bar.
Excluded from this version are:
- All group 0 motors
- Group 1 motors centering ø32 for CF001 shaft, centering ø30 and ø50.8 mm
- Group 2 motors centering ø52 for CF001 shaft
Other particular solutions
In addition to the customizations just seen, you can also plan for:
1 – The support with bearings
It increases resistance to radial and axial loads. It is recommended when objects with high masses are to be rotated.
2 – Anti-cavitation valve
It is used when it is necessary to prevent, even unintentionally, the motor from rotating in the opposite direction than intended.
It can therefore be applied only in unidirectional motors.
It prevents, for example, bouncing related to inertial loads.
Also, in case the outlet is blocked, it allows the motor to rotate by sending oil back into the motor inlet (bypass).
3 – Pressure relief valve
Limits the pressure at the load of the hydraulic motor and protects it from damage caused by pressure spikes.
4 – Anti-cavitation valve + relief valve
It combines the effects of both options. Clearly, even this mode is only possible in unidirectional motors.
5 – Speed controller
It allows direct control of the rotational speed of the motor shaft by operating a cutoff on the flow rate.
6 – External drainage for unidirectional motors
It is used to preserve the internal seals of the motor from pressure in the drain line. Normally, the use of a reversible motor is suggested.
7 – Fan drive
System that includes, in the motor itself, flow and pressure control systems that, through interpreted signals, allow action in response to adjust the speed and possibly the direction of rotation.
It is normally applied to cooling fans.
8 – Double cross relief valve
System that allows the presence of a pressure-limiting valve for each direction of rotation.
9 – High pressure shaft seal
A different solution from the standard oil seal, it is in fact an oil seal with a higher pressure seal whose value depends on the size group: up to 20-25 bar continuous at 1500 rpm.
This value decreases as the rotation speed increases.
It is recommended in unidirectional motors with drainage pressures up to 25 bar and in reversible motors for drainage pressure up to 25 bar.
Currently, it is available on Group 1, 2 and 3 motors.
10 – VITON® Seals
They are elastomers other than normal NBR, which have better properties and resistance to high temperatures.
11 – Electric bypass valve
It deflect oil flow from the inlet directly to the motor exhaust. The valve is actuated by an external electrical signal.
To learn more about when and how to use these options, read our guide to special solutions for Vivoil motors.
How to install the Vivoil motor and directions for use
Having chosen the motor, here are the steps to install it and some tips for its maintenance.
Installing the hydraulic motor
1) Preliminary Checks
- Check that the direction of rotation matches the connections
- Check that the coupling flange is properly aligned with the drive shaft and the drive shaft
- Check that the fittings are flexible and not rigid, to avoid generating loads on the inlet and outlet ports
2) Tank arrangement
- Ensure that the tank capacity is about 3-5 times the amount of oil handled, i.e., enough to operate the system and avoid overheating of the fluid
- If necessary, install a heat exchanger
- Insert a vertical divider to distance the tank return suction pipes and prevent oil from being re-injected immediately
3) Pipe arrangement
- Check that the diameter of the pipes is greater than or equal to that of the motor fittings and that the pipes are sealed
- Check that the pipes are perfectly clean and short
- Minimize hydraulic sources of resistance (elbows, throttling valves, and others) to avoid power loss
- However, it is recommended to provide a section of flexible pipe to reduce vibration transmission
- Check that all return pipes end below the minimum oil level to avoid foaming
- Before connecting the pipes, remove any plugs
4) Drain port configuration
- When present, the drain line must be connected to the tank
- If a reversible motor with a drain port is to be used as a unidirectional motor without connecting the drain to the tank, the rear cover must be replaced or the drain must be routed to a zero or low-pressure area (such as the tank)
- When motors are used in series, it is essential that each one is equipped with a drain line, and that all drain lines are connected to the tank
5) Filter installation
- Filter the entire system flow
- Install suction and return pipe filters according to the contamination class indicated in our catalogs
6) Selection of hydraulic fluid
- Use a hydraulic oil conforming to ISO/DIN standards and of the same viscosity as indicated in our catalogs
- Avoid mixtures of different oils because they may reduce the lubricating power of the fluid
Changing the valve range
Changing the valve range is useful if the operating conditions are different from those estimated or have changed over time, because the range should be defined according to the pressure at which the motor is used. To change it, simply replace the spring found inside the valve with one of a different size, to be selected according to the size group. We have prepared a guide on how to change the range of Vivoil valves that will help you with the change depending on the type of valve used in your motor.
Starting the motor
- Check that all circuit connections are tight and that the whole system is completely clean
- Insert the oil into the reservoir, using a filter
- Purge the circuit to facilitate filling
- Set safety valves to the lowest possible pressure
- Turn on the system for a few seconds at minimum speed, then purge the circuit again and check the oil level
- Gradually increase pressure and rotational speed where possible until operating levels are reached
Hydraulic motor maintenance and repair
To check the proper operation of the hydraulic motor you have installed, we recommend:
- Keep the outer surface clean, especially in the drive shaft seal area, because abrasive dust can accelerate seal wear and cause leaks
- Change filters regularly to keep the fluid clean
- Check the oil level and replace it periodically, depending on the operating conditions of the system
How to replace the Vivoil component you already have with a new one
Vivoil motors have labels identifying the product so you can request a replacement if needed. If you have a Vivoil motor from the old KV series that has come to the end of its life and you need to replace it with a new one, you can choose a motor from the new series. If you have any difficulties, we are available to help you with correct identification.
Most common problems in motor use
The most common problems that can occur using a hydraulic motor are:
Ejection of the shaft seal
The shaft seal is a seal located near the shaft. When the pressure on the drain is too great or when the motor supply is in the wrong direction or the drain pressure exceeds the maximum allowed, this seal can break or come off. To solve the problem, simply replace the damaged shaft seal with a new one. Want to learn more? Read our article on what are the most common causes in oil leaks in motors.
Shaft breakage
Each type of shaft has, by its shape and size characteristics, a torsional strength value that is given on the relevant catalog pages.
In the event that the motor works at excessive pressures or under significant cyclic loads, this can lead to shaft failure or, in the case of a tapered or parallel shaft, key failure.
In these cases, it is important to verify the correct assembly of the coupling and working conditions.
Breakage of the motor body
In the event that the motor operates at excessive pressures or under significant cyclic loads, it can result in body rupture. Available solutions include ports that have a greater capacity to withstand cyclic stresses.
Excessive temperatures
If the temperature exceeds the levels given in our catalogs, the motor may be damaged.
Dirt damage
The presence of impurities in the oil damages the internal surfaces of the motor to the point of worsening its operation/performance.
Drain port closure
The drain port, when present, must not be plugged.
Even when a reversible motor is used as a unidirectional motor.
This is because the unidirectional version of the rear cover includes a hole that connects the area behind the shaft seal to the outlet (i.e., a zero or very low-pressure area). If the drain port is blocked, the shaft seal will be pushed out.
If a reversible motor with a drain port is used as a unidirectional motor and you do not wish to connect the drain to the tank, the rear cover must be replaced, or the drain must be connected to a zero or low-pressure area (such as the tank).
When using motors in series, the version with external drainage must be used, and all drains must be properly connected to the tank.
Special applications of our motors (out of common use)
Here are some of the more special applications of our hydraulic motors:
- Series (or multiple) motors are connected to each other and work in sequence.
- CY Vivoil motor-pump assembly, indicated when the application generates residual oil flow, which can be used to achieve energy savings and recover power. Instead of opting for a pump connected to a hydraulic motor, you can choose a single component with integrated motor and pump.